Multiple Effect Evaporation
- Home
- Evaporation Crystallization System
- Multiple Effect Evaporation
Working Principle
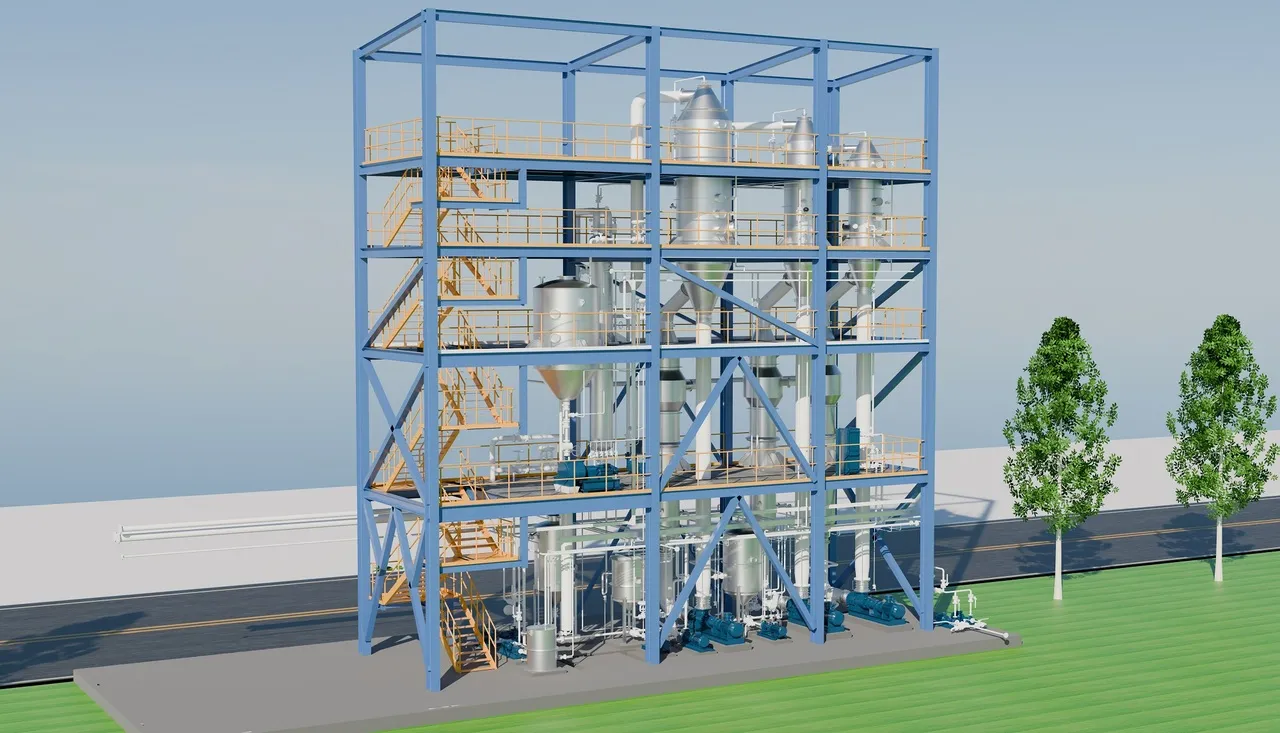
Highlight Features of Multiple Effect Evaporation
Energy Savings
Process Diversity
Cost Efficiency
Adaptable Handling
Operational Flexibility
System Scalability
Evaporation and Crystallization for Various Industries
Efficient Manufacturing
A self-owned manufacturing base of 130,000㎡, equipped with advanced equipment and automation systems.
Full Lifecycle Solutions
Comprehensive solutions covering design, civil engineering, automation, R&D, production, delivery, commissioning, and after-sales support.
Technical Team Support
400+ engineers with 5+ years of experience providing expertise in process engineering, civil design, and automation control systems.
Custom Design
Providing comprehensive project planning, process design, 3D design, civil engineering design to meet specific project requirements.
Process Optimization
Employs low-temperature MVR evaporation, flash evaporation, and cooling crystallization to optimize energy efficiency and ensure high-quality crystals.
After-Sales Service
Free repairs and parts replacement within an 18-month warranty, with timely technical and localized support from our overseas team.