Introduction
Hello, I’m Alex, and I have spent many years in the process engineering field working with Myande Group. Our company has over 20 years of experience in providing turnkey evaporation crystallization solutions. I have seen firsthand how falling film evaporators transform heat-sensitive liquid concentration. Today, I want to share my personal insights on the design and manufacturing of these efficient systems. I understand the challenges you face and the pressure to reduce energy consumption while maintaining product quality.
In this article, I will share my insights and practical experience on the design and manufacturing of falling film evaporators, emphasizing key components, operating principles, and maintenance tips. This information is valuable for anyone looking to improve efficiency, reduce energy consumption, and ensure high product quality in their industrial processes.
As I continue to explain these concepts, I invite you to explore the details with me. I will discuss the critical criteria in design, explain how to improve efficiency, and provide some unique insights gathered over years of hands-on work. Let’s dive in and see how these evaporators can work wonders in your processes.
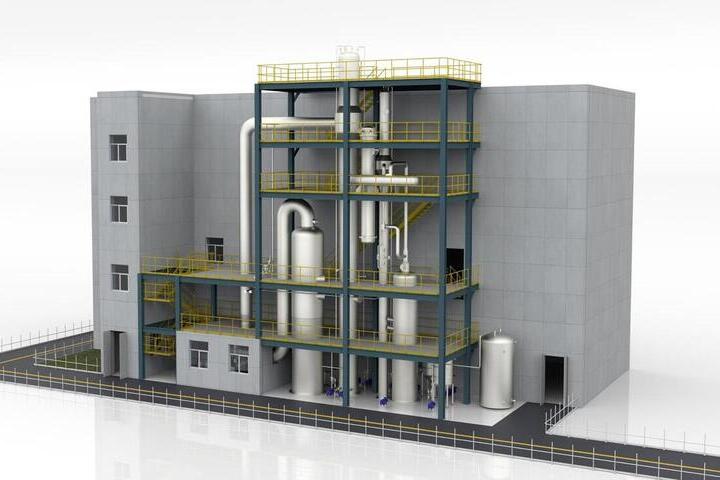
Key Components at a Glance
To help you quickly understand the essentials, here is a table summarizing the key components of a falling film evaporator:
Component | Function | Benefit |
Heat Exchanger | Transfers heat from the external medium to the liquid film | Enhances evaporation efficiency |
Liquid Distributor | Evenly spreads the feed liquid over tube surfaces | Prevents dry spots and reduces fouling |
Vapor Separator | Separates vapor from concentrated liquid at the bottom | Maintains operational efficiency |
Cleaning Systems (CIP) | Circulates cleaning solutions to remove deposits and scale | Reduces maintenance downtime |
This table not only clarifies the function of each component but also supports our discussion with a structured summary that is easy to reference.
What Are the Criteria for Falling Film Evaporator Design?
When designing a falling film evaporator, I always start by considering a few fundamental criteria. I have learned through experience that every detail counts. The success of the design depends on balancing efficiency, reliability, and ease of maintenance. In our projects at Myande Group, we emphasize the importance of understanding these criteria to avoid common pitfalls that lead to fouling and operational downtime.
The design criteria include maximizing heat transfer efficiency, ensuring a uniformly thin liquid film across the tubes, selecting corrosion-resistant materials with high thermal conductivity, and maintaining precise control over operational parameters such as temperature and pressure. In addition, a well-designed liquid distribution system is essential to prevent uneven wetting and localized overheating, while an effective vapor separator minimizes the risk of carryover.
I find that when these criteria are met, the overall performance and reliability of the evaporator are greatly enhanced. For instance, by optimizing the tube diameter and length, we can significantly increase the surface area available for heat transfer. Furthermore, using materials like AISI 316-L stainless steel not only resists corrosion but also supports sustained high thermal conductivity. In my experience, careful attention to operational parameters, such as vacuum conditions that lower boiling points for heat-sensitive products, leads to better process control and energy savings. These design choices ensure that our systems run efficiently, with minimal maintenance interruptions.
How to Improve Falling Film Evaporator Efficiency?
Improving efficiency has always been a top priority in my work. I constantly look for innovative ways to enhance performance and reduce energy costs. In my projects, every small improvement adds up to a significant overall gain in efficiency. From the initial design to routine maintenance, every step matters.
Enhancing efficiency involves increasing the heat exchange area by optimizing tube geometry, applying advanced coatings, and ensuring a uniform liquid distribution across the entire surface. It also means refining operational parameters such as inlet temperature differences and pressure control. Regular use of cleaning-in-place (CIP) systems to prevent fouling further boosts performance.
In addition, I have observed that adopting computational fluid dynamics (CFD) in the design phase can provide a detailed understanding of flow dynamics within the evaporator. This technology helps to simulate various scenarios and optimize the liquid film behavior. Moreover, by integrating advanced control systems, we can monitor temperature, pressure, and flow rates in real time, allowing us to make adjustments that further improve efficiency. These improvements not only reduce energy consumption but also help maintain the quality of the final product. I have seen these strategies work wonders in many of our installations, making the process more robust and cost-effective.

Additional Insights and Applications
Over the years, I have gathered unique insights that go beyond standard design considerations. I want to share a few of these practical experiences that may be useful for you as well.
Importance of Material Selection
Material selection plays a pivotal role in the long-term success of an evaporator. I have seen projects where the wrong material choice led to frequent maintenance and downtime. At Myande Group, we always choose corrosion-resistant materials such as AISI 316-L stainless steel. This choice is critical, especially when handling aggressive liquids. Additionally, materials with high thermal conductivity ensure that heat is transferred rapidly and efficiently. If you want to learn more about material choices in heat exchangers, the Engineering Toolbox website offers some practical guidelines.
Optimizing Liquid Distribution
A uniform liquid film is key to efficient heat transfer. In my experience, even a small imbalance in liquid distribution can lead to significant performance issues. To tackle this, we focus on designing sophisticated liquid distributors that ensure even spread across all tubes. This design aspect is especially important in large-scale operations where even minor discrepancies can lead to severe fouling problems. Uniform distribution not only improves heat transfer but also extends the service life of the equipment. Moreover, I always recommend regular inspections to confirm that the distributor continues to perform as intended.
Continuous Operation and Maintenance
Continuous operation capability is crucial in industrial applications. I always emphasize the need for a robust cleaning system integrated into the design. Cleaning-in-place (CIP) systems are invaluable as they reduce downtime and maintain efficiency. In one of our projects, implementing an effective CIP system cut maintenance time by nearly 30%. This improvement not only saved time but also significantly reduced the cost of operation over the long term. Regular maintenance and proper operational training for your team can prevent many common issues that arise in evaporators. These practices have proven beneficial in my career and can be the difference between a smooth operation and a costly shutdown.
Applications Across Industries
Falling film evaporators are versatile and are used in many industries. I have seen them successfully applied in the food and beverage sector, pharmaceutical manufacturing, and even wastewater treatment. For instance, in the food industry, these evaporators concentrate juices and dairy products without compromising their delicate flavors and nutritional content. In the pharmaceutical field, they help in concentrating extracts while preserving their integrity, thanks to the low residence time. Moreover, in wastewater treatment, they enable efficient contaminant concentration, contributing to environmental sustainability. Their versatility is one of the reasons why I believe they are an indispensable asset in modern industrial processes.
Real-World Success Stories
I recall a project where we redesigned an existing falling film evaporator to better handle a highly sensitive liquid used in food processing. By optimizing the tube geometry and incorporating a more effective liquid distribution system, we increased the heat transfer efficiency by 20%. This improvement allowed our client to reduce energy consumption while maintaining product quality. Such success stories are a testament to the importance of thoughtful design and continuous improvement. They also highlight the potential benefits that you, as a reader, can achieve by applying these insights to your own processes.
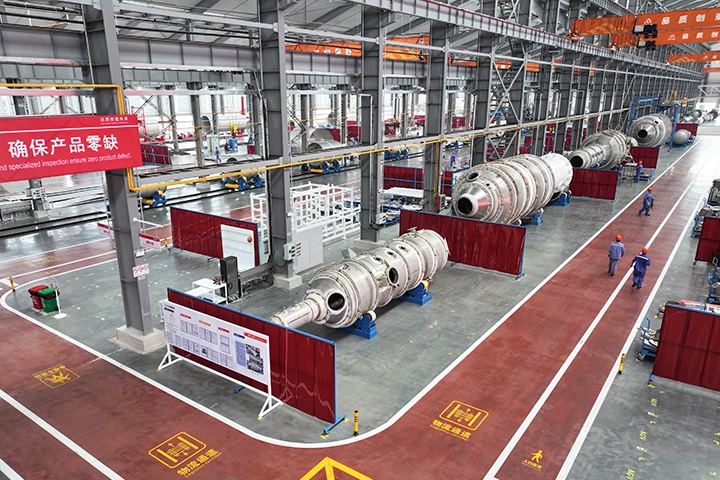
Conclusion
In summary, designing and manufacturing efficient falling film evaporators requires careful attention to several key factors. I have shared with you the essential criteria for designing these systems—maximizing heat transfer efficiency, ensuring uniform liquid distribution, and selecting the right materials and operational parameters. Equally important is the continuous effort to improve efficiency through advanced simulation, optimized geometry, and diligent maintenance practices.
I hope that the insights I have provided here give you a clearer picture of the design process and help you make informed decisions for your projects. Whether you are looking to upgrade an existing system or install a new one, I encourage you to apply these strategies. By doing so, you can achieve significant improvements in energy savings, operational reliability, and product quality.
For further reading, I recommend checking out the following external resources:
ScienceDirect – Falling Film Evaporation
Engineering Toolbox – Evaporators
Wikipedia – Evaporator
Thank you for taking the time to read my article. I am confident that with these insights, you can enhance your processes and achieve better efficiency. Please feel free to reach out if you have any questions or need further assistance—we at Myande Group are always here to help you succeed.