Fertilizer producers today face enormous pressure. Whether it’s rising raw material prices, water scarcity, or tightening emissions regulations, delivering high-performance, cost-effective, and environmentally sustainable products is more complex than ever.
Evaporators and crystallizers play a vital role in optimizing fertilizer production by concentrating, purifying, and recovering valuable nutrients while minimizing energy use and waste.
I’ve worked alongside engineers and operations managers in fertilizer plants around the world, and the most effective operations consistently rely on modern evaporation and crystallization systems to stay competitive. Let me show you how and why.
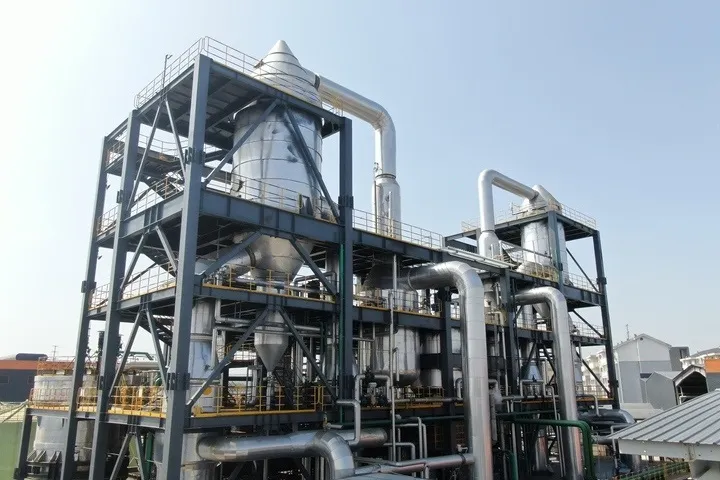
What Role Do Evaporators and Crystallizers Play in Fertilizer Production?
These systems aren’t just mechanical tools; they are the backbone of modern fertilizer refining and recovery processes.
Evaporators are used to reduce water content and increase nutrient concentration, while crystallizers transform dissolved nutrients into pure, solid fertilizers.
Let’s explore where and how they make a difference:
Key Applications in Fertilizer Production
Technology | Purpose | Example Application |
---|---|---|
Evaporator | Liquid concentration | Ammonium nitrate to 95% solids |
Evaporator | Phosphoric acid upgrade | From 30% to 54% P₂O₅ |
Crystallizer | Solid nutrient recovery | SOP from potassium-rich brine |
Crystallizer | Wastewater treatment | ZLD from high-salinity streams |
These applications help reduce transport costs, increase product purity, and improve environmental compliance.
Why Are These Technologies So Effective in Fertilizer Manufacturing?
When applied strategically, evaporation and crystallization systems can help you achieve multiple goals at once—from energy savings to product differentiation.
They concentrate and crystallize nutrients efficiently, recover resources from waste, and reduce your operational footprint.
Let’s break down the benefits:
Key Advantages
- Energy Efficiency: MVR evaporators cut energy use by up to 90% compared to thermal alternatives.
- Customization: You can control crystal size and purity to suit different market needs.
- Sustainability: These systems support circular economies by recovering water and reducing discharge.
- Versatility: Suitable for both synthetic (e.g., urea) and organic (e.g., digestate) fertilizers.
Modern systems also support automation, scalability, and modular expansion.
Real Industry Use Cases
I’ve seen firsthand how Myande’s evaporation and crystallization systems help fertilizer producers worldwide adapt to complex processing challenges. Here are just a few examples:
1. Nitrogen-Based Fertilizers
- Evaporators concentrate urea or ammonium nitrate post-synthesis.
- Crystallizers recover ammonium sulfate from by-product streams in nickel or caprolactam production.
2. Phosphate-Based Fertilizers
- Evaporation increases phosphoric acid concentration from 30% to 54% P₂O₅.
- Crystallization is used in MAP/DAP production to combine ammonia and phosphoric acid precisely.
3. Potassium-Based Fertilizers
- SOP production via brine lake crystallization avoids furnace-based systems.
- Cooling crystallizers yield high-purity MOP from solution-mined KCl.
4. Organic Fertilizers
- Digestate evaporation reduces slurry volume and concentrates nutrients.
- Crystallizers help recover solid NPK components from liquid organics.
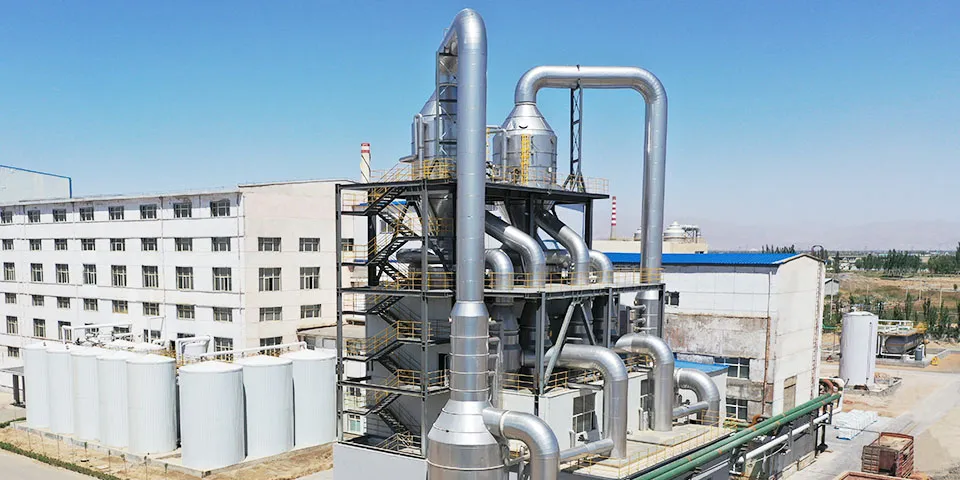
What is the Application of Evaporative Crystallizer?
Evaporative crystallizers are fundamental in fertilizer production—but their usefulness extends far beyond it.
They concentrate solutes by evaporating the solvent, eventually forming high-purity crystals used in commercial fertilizers and other products.
Typical applications include:
Industry | Application Example |
Fertilizer | Ammonium sulfate, SOP, MAP/DAP |
Chemicals | Salt, acid, and base purification |
Food | Sugar and salt crystallization |
Pharma | API crystallization and separation |
Waste Treatment | ZLD, water reuse, solids recovery |
Crystallizers are ideal for ZLD systems, nutrient recovery, and producing customizable fertilizer products.
What Is an Evaporator in the Chemical Industry?
You might be asking, “Isn’t this just for chemicals?” But fertilizer is chemistry, and the tools we use are universal.
An evaporator is a heat exchanger that concentrates liquids by converting part of them to vapor, leaving behind a more concentrated solution or solid.
In fertilizer plants, this means removing water from nutrient slurries, purifying process liquids, or preparing materials for crystallization.
Core Applications
Function | Purpose |
Solution concentration | Increase fertilizer nutrient content |
Solvent recovery | Reclaim valuable liquids for reuse |
Waste reduction | Minimize disposal costs |
Feed preparation | Prepare inputs for crystallization |
Evaporators can be single-effect, multi-effect, or MVR types depending on your scale, energy source, and process needs.
Final Thoughts: Is It Time to Rethink Your Fertilizer Process?
Evaporation and crystallization are no longer niche solutions. They are essential technologies for fertilizer producers aiming to reduce waste, optimize output, and stay compliant with environmental regulations.
If you’re ready to improve efficiency, recover more resources, and build a more sustainable fertilizer operation, now is the time to act.
At Myande Group, we bring decades of engineering experience and world-class manufacturing capabilities to every project. Whether you need a standalone evaporator or a complete turnkey fertilizer production line, we’re here to help.