If you’re exploring sustainable and cost-effective evaporation technologies, especially in industries like lithium extraction, chemical recycling, food processing, or zero liquid discharge, you may have heard of MVR evaporators. I’m often asked by clients—both new and experienced in industrial operations—what makes MVR so different, and whether it’s truly worth the investment.
An MVR (Mechanical Vapor Recompression) evaporator recycles vapor by compressing it and using it as a heat source, drastically cutting energy consumption by up to 90% compared to traditional systems.
That level of efficiency can completely reshape your operating costs and carbon footprint. And while the technology might sound complex at first, once you understand how it works—and how it compares to systems like TVR or multi-effect evaporators—you’ll see why it’s gaining traction across so many sectors.
What is an MVR Evaporator?
MVR stands for Mechanical Vapor Recompression. It’s an energy-saving evaporation technology where vapor produced during the evaporation process is mechanically compressed and reused as the heat source.
This closed-loop heat recycling significantly reduces the need for external steam, improving energy efficiency and lowering operational costs.
At Myande, we’ve implemented MVR systems across various industries—from salt recovery to bio-fermentation—helping customers minimize environmental impact while maintaining high evaporation performance.
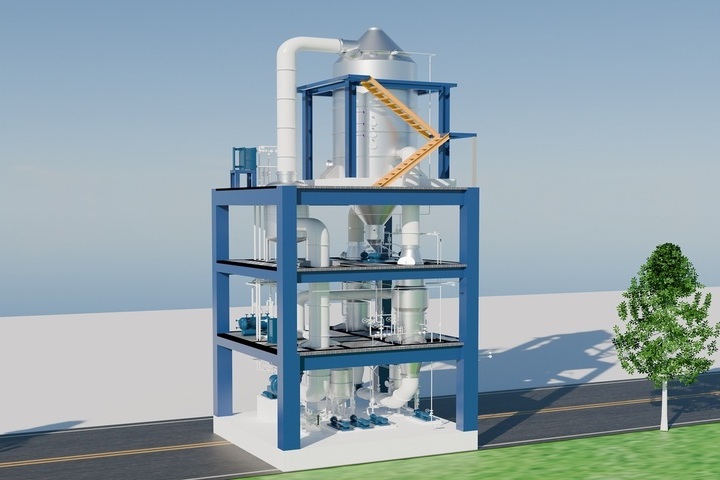
How Does an MVR Evaporator Work?
The working principle of MVR evaporators is similar to that of a heat pump.
The vapor generated during boiling is compressed using a mechanical compressor or fan. This increases its temperature and pressure, allowing it to be reused for further evaporation in the system.
This process dramatically reduces energy input by replacing most of the external steam or heat source. It also supports better temperature control and reduces thermal degradation of sensitive materials.
What Are the Advantages of MVR Evaporators?
MVR evaporators come with several compelling advantages that can boost both sustainability and profitability.
Advantage | Description |
---|---|
Energy Efficiency | Up to 90% lower energy consumption vs. traditional evaporators |
Lower Operating Costs | Lower utility bills and reduced steam dependence |
Gentle Processing | Low temperature differential preserves product integrity |
Compact System Design | Smaller footprint compared to multi-effect systems |
Automated Control | Easy operation and stable performance |
In summary, MVR offers a win-win: cost savings and a smaller carbon footprint.
That’s why industries like dairy, lithium, and wastewater treatment are shifting towards MVR technology. We’ve seen clients save thousands annually while also achieving stricter environmental compliance.
What Are the Applications of MVR Evaporators?
MVR evaporators are highly adaptable across industries. At Myande, we’ve delivered successful MVR solutions in:
- Industrial Wastewater Treatment: For zero liquid discharge (ZLD) and heavy metal removal
- Food & Beverage: For concentration of juices, syrups, and heat-sensitive products
- Bio-Fermentation: In lysine, citric acid, and xanthan gum production lines
- Lithium & Salt Recovery: Recovery and concentration in lithium extraction, including ore and brine
Their ability to recycle energy and reduce effluent makes them a preferred choice in both greenfield and brownfield projects.
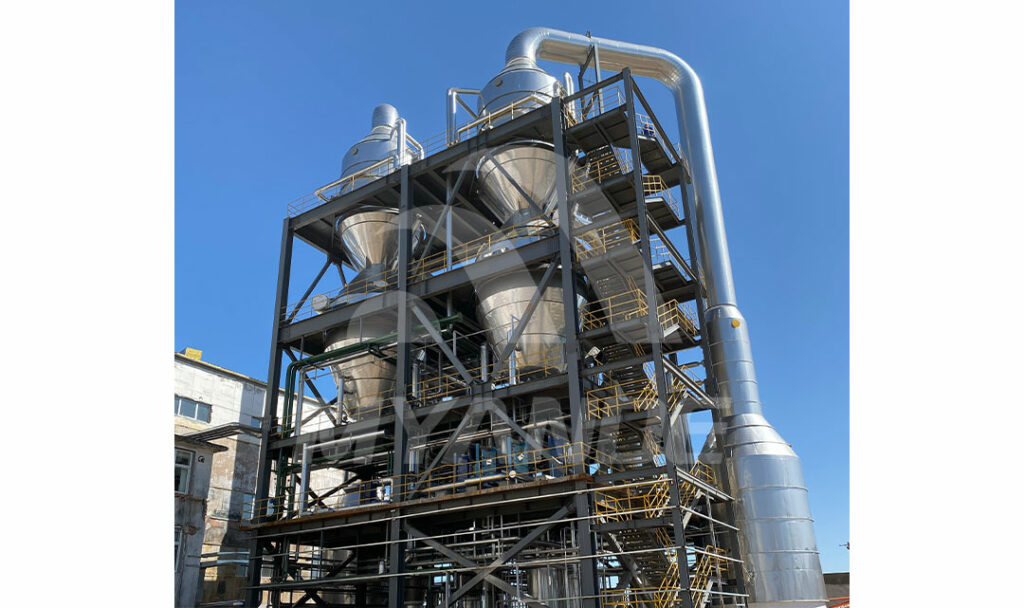
How Do MVR Evaporators Compare to TVR Evaporators?
MVR and TVR (Thermal Vapor Recompression) are both vapor recompression technologies—but they differ significantly.
MVR uses electricity to compress vapor, while TVR uses high-pressure steam. MVR is typically more efficient but also requires higher initial investment.
If energy cost, space, and long-term ROI matter to your operation, MVR is usually the better fit. On the other hand, TVR might suit facilities with an abundant steam supply and low power infrastructure.
What Are Common Problems and Solutions?
Even advanced systems like MVR can run into issues. Fortunately, most are manageable with proper design and maintenance.
Problem | Common Cause | Solution |
---|---|---|
Scaling/Fouling | Hard water or high TDS in feed | Use acid wash or soft water; pre-treatment |
Boiling Point Rise | High solute concentration | Optimize feed rate and vacuum pressure |
Vacuum Leaks | Gasket failure or design flaws | Regular inspection, replace seals |
Preventative maintenance and robust system design are key to avoiding these headaches.
At Myande, we customize MVR systems to handle varying feed characteristics and include CIP (clean-in-place) options to reduce downtime.
How to Choose the Right MVR Evaporator System?
Choosing the right system means considering several practical factors:
- Energy Cost & Availability: Can your facility support consistent electricity usage?
- Product Properties: Is your product heat-sensitive or viscous?
- Evaporation Rate: What capacity do you need?
- Space Constraints: MVR units typically have a smaller footprint
A tailored consultation can help you choose a system that meets your technical and budget goals.
At Myande, we offer simulation, 3D design, and energy audits as part of our turnkey services to ensure the right fit for every client.
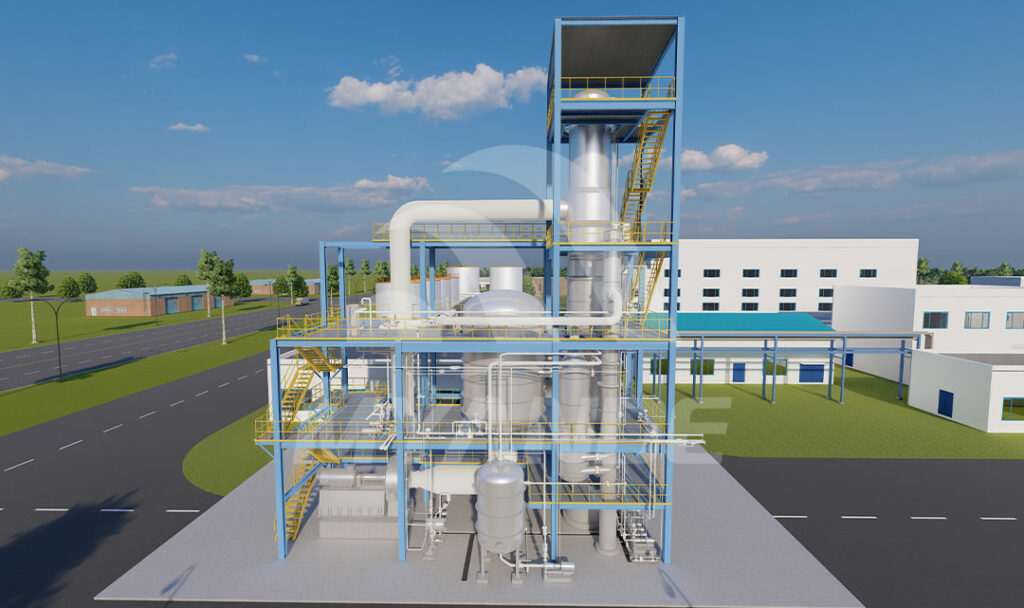
What is the Efficiency of MVR?
Efficiency is where MVR evaporators really shine.
Studies show MVR systems use only 0.06 kWh to evaporate 1 kg of water. That’s about 193 pounds of water per kWh—making MVR one of the most energy-efficient solutions available.
Compared to TVR or single-effect systems, MVR saves up to 90% on energy. And since it uses electricity instead of steam, it’s also easier to integrate into renewable energy sources like solar or wind.
MVR vs. TVR: Detailed Comparison
Here’s a quick reference table to help you evaluate which system fits your needs:
Feature | MVR | TVR |
---|---|---|
Energy Source | Electricity | High-pressure steam |
Energy Savings | 70–90% | 30–50% |
Investment Cost | Higher upfront | Lower upfront |
Maintenance | Requires trained staff (compressor) | Low (no moving parts) |
Footprint | Smaller | Larger |
Flexibility | High | Depends on steam availability |
MVR is ideal for facilities prioritizing sustainability, long-term savings, and flexible operation.
Factors Affecting Multiple-Effect Evaporators
Multiple-effect evaporators (MEE) are commonly used, but their performance is sensitive to several factors:
- Material Properties: Viscosity, density, and boiling point elevation impact heat transfer
- Process Conditions: Feed concentration, flow rate, and vacuum levels determine performance
- Environmental Factors: Altitude and cooling water availability affect condenser operation
- Fouling & Scaling: These reduce efficiency and increase cleaning frequency
Proper system design and smart controls can greatly improve MEE efficiency and reduce operating costs.
If your process requires large throughput but with moderate energy savings, MEE might be the right fit—or pair it with MVR for hybrid efficiency.
Final Thoughts
At Myande Group, we’ve seen firsthand how MVR evaporators can elevate industrial performance. From lower emissions and energy use to easier compliance and better product quality, the benefits are clear.
If you’re considering upgrading or investing in evaporation systems, let’s have a conversation. Our team is here to help—from process design to commissioning and after-sales support.
For more real-world examples, feel free to explore our project cases or request a consultation directly.