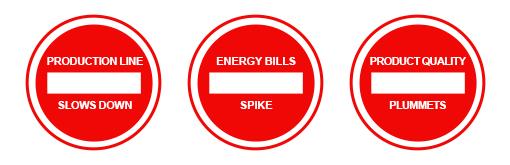
Imagine this: your production line suddenly slows down, energy bills spike, and product quality plummets. The culprit? A clogged evaporator. This is not just an inconvenience; it’s a significant threat to your efficiency, product consistency, and profitability. If left unchecked, a clogged evaporator can lead to extended downtime, costly repairs, and substantial financial losses. The frustration and stress of frequent breakdowns can be overwhelming, but there’s a way to address this issue head-on.
Signs of a Clogged Evaporator
Recognizing the symptoms of a clogged or fouled shell and tube evaporator early can save you time and money. Here are the key indicators:
1. Decreased Evaporation Rate: When your evaporator is clogged, the flow of feed liquid over the heat transfer surfaces is restricted. This reduction in flow rate directly impacts the overall evaporation rate and throughput of the system. If you notice a decline in your evaporator’s performance, it might be due to clogging.
2. Increased Pressure Drop: As fouling builds up on the tube surfaces, it creates flow restrictions, leading to an abnormal increase in pressure drop across the evaporator. Monitoring the pressure differential can help identify this issue.
3. Poor Heat Transfer: Fouling deposits act as an insulating layer, reducing heat transfer efficiency. This can be detected by uneven temperature distribution or localized hot spots on the evaporator surface. Reduced heat transfer can significantly affect the efficiency of your process.
4. Frequent Cleaning Required: If you find yourself needing to perform chemical cleaning cycles more frequently, such as acid cleaning, to maintain performance, it is a clear sign of fouling buildup. This indicates that your evaporator is not functioning optimally and requires more attention.
5. Visible Scaling/Fouling: If you can visually inspect the evaporator tubes and the shell side, look for the buildup of scales, precipitates, or fouling deposits. Visible signs of scaling are a direct indicator of clogging and fouling.
6. Inconsistent Product Quality: Clogging can lead to uneven liquid distribution and heating, resulting in inconsistent concentration or quality of the evaporated product. Variations in product quality are a significant red flag indicating problems within the evaporator.
7. Increased Energy Consumption: As fouling increases, more energy is required to compensate for the poor heat transfer, leading to higher utility costs. If you notice a sudden increase in energy consumption without a corresponding increase in production, it could be due to a clogged evaporator.
Regular monitoring of key performance parameters like flow rates, temperatures, pressures, and energy consumption is crucial for early detection of evaporator clogging. Implementing a preventive maintenance schedule based on the nature of the feed stream can help mitigate fouling issues and keep your evaporator running efficiently.
Understanding the symptoms of a clogged evaporator is just the beginning. To maintain optimal performance and avoid costly downtime, it’s essential to know how your evaporator works and how to clean it effectively. By delving deeper into the operation and maintenance of shell and tube evaporators, you can ensure your equipment remains in top condition, providing reliable and efficient service.
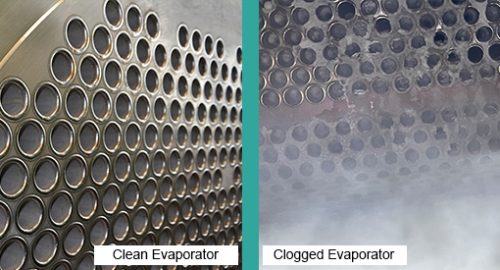
How Does a Shell and Tube Type Evaporator Work?
A shell and tube type evaporator is a specific configuration of a shell and tube heat exchanger used for evaporation processes. Here’s a detailed look at how it works:
Basic Structure
1. Tube Bundle: The evaporator consists of a bundle of tubes enclosed within a cylindrical shell.
2. Fluid Flow: The fluid to be evaporated (feed liquid) flows through the tubes, while the heating medium (steam, hot fluid, etc.) flows over the outer surface of the tubes within the shell.
Flow Arrangement
1. Feed Liquid Entry: The feed liquid enters the tube bundle through an inlet nozzle in the tube sheet at one end.
2. Flow Through Tubes: The feed liquid flows through the tubes, where it is heated and partially/fully evaporates.
3. Exit of Vapor and Liquid: The vapor and any remaining liquid exit through an outlet nozzle at the other end of the tube bundle.
4. Heating Medium Flow: The heating medium enters the shell through an inlet nozzle, flows across the tube bundle in a specific pattern aided by baffles, and exits through an outlet nozzle.
Heat Transfer Process
1. Heat Transfer: Heat is transferred from the hot heating medium to the cooler feed liquid through the tube walls.
2. Evaporation: As the feed liquid flows through the tubes, it absorbs heat, causing a portion of it to vaporize (evaporate).
3. Evaporation Factors: The degree of evaporation depends on factors like the heat transfer area, flow rates, and temperature differences.
Multi-Pass Design
1. Efficiency Improvement: To increase heat transfer efficiency, the tube bundle can be designed for multiple passes, where the fluid makes multiple passes through different sections of the tube bundle.
2. Heat Transfer Length: This increases the effective heat transfer length and improves evaporation rates.
Baffles and Tube Arrangements
1. Flow Direction: Baffles are installed in the shell to direct the flow of the heating medium across the tube bundle and induce turbulence, enhancing heat transfer.
2. Tube Patterns: Tube arrangements like triangular or rotated square patterns are used to optimize heat transfer and fluid flow.
Shell and tube evaporators are widely used in various industries, such as chemical processing, lithium extraction, food and beverage, pharmaceutical, and desalination plants, for concentrating or evaporating liquids. Their design can be customized based on the specific process requirements, heat transfer rates, and desired evaporation rates.
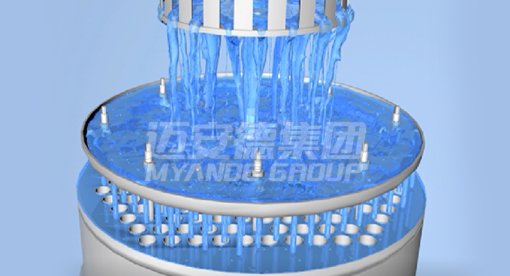
How Do You Clean a Shell and Tube Evaporator?
Cleaning a shell and tube evaporator is essential to maintain its efficiency and longevity. Here are the typical methods used to clean these evaporators:
Mechanical Cleaning
1. Tube Lancing/Rodding: A rodding machine is used to clean the evaporator tubes by propelling flexible lances or rods at high pressure (up to 10,000 psi) to dislodge fouling and deposits from the inside of the tubes.
2. Tube Brushing/Drilling: Mechanical brushes or drilling tools can be inserted into the tubes to scrape off and remove hard deposits.
Chemical Cleaning
A closed-loop chemical cleaning system is used to circulate chemical solutions (acidic or alkaline) through the evaporator to dissolve and remove scales, fouling, oil/grease deposits. The steps typically involve:
1. Preparation: Isolating and preparing the evaporator by removing covers/heads.
2. Chemical Circulation: Circulating the heated chemical solution through the tube side and shell side using pumps.
3. Solution Monitoring: Monitoring solution strength and replenishing/adjusting as needed.
4. Rinsing: Rinsing with clean water to remove chemical residues.
Water Jetting
High-pressure water jetting (up to 2500 bar or 36,000 psi) can be used to blast away fouling from the inside of the tubes using flexible lances or rigid lances mounted on tube lancing equipment (TLE). The key steps include:
Isolation: Shutting down and isolating the evaporator.
Access: Removing heads/covers to access the tube bundle.
Jetting: Deploying high-pressure water jetting lances into the tubes.
Waste Management: Collecting and treating the wastewater generated.
Regular cleaning intervals (e.g., every 3 years for evaporators) are recommended to maintain efficiency and prevent excessive fouling buildup. Proper planning for downtime, safety precautions, and waste handling is crucial for effective evaporator cleaning.
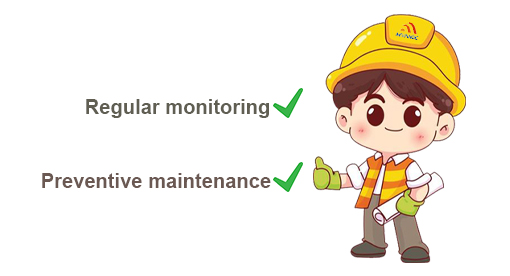
Conclusion
Maintaining your evaporator in peak condition is essential for ensuring efficient operation, consistent product quality, and cost-effective production. By understanding the signs of clogging, the working principles of shell and tube evaporators, and effective cleaning methods, you can prevent downtime and extend the life of your equipment. Regular monitoring and preventive maintenance are your best allies in keeping your evaporator running smoothly and your production line efficient. Remember, a proactive approach to maintenance can save you from significant headaches and expenses down the line.