Today’s industrial producers face mounting pressure—from skyrocketing energy prices to tightening environmental regulations. Whether you’re in chemical manufacturing, food processing, lithium extraction, or wastewater treatment, you’ve likely felt the squeeze. And let’s be honest: Traditional evaporation systems just don’t cut it anymore when efficiency and sustainability are on the line.
If you’re looking for a smarter way to concentrate, recover, or treat, Mechanical Vapor Recompression (MVR) evaporation could be the breakthrough your operation needs. It’s not just another piece of equipment—it’s a new mindset for sustainable, cost-effective industrial processing.
At Myande Group, I’ve spent the past 20 years helping clients around the world transition to MVR systems. In this article, I’ll walk you through what makes MVR special, how it works, and why it’s changing the game for industries like yours.
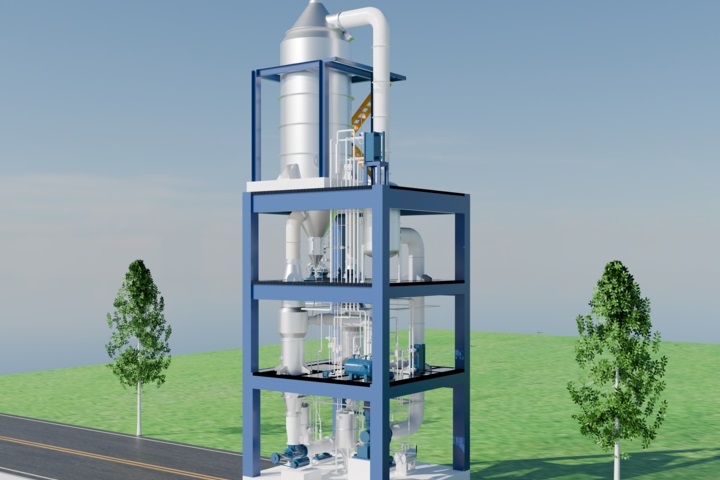
What is the MVR Evaporator Process?
When I talk to engineers and plant managers about MVR, the first thing they ask is usually: “How exactly does it work?”
The MVR evaporator process recycles vapor heat through mechanical compression, making it one of the most energy-efficient thermal separation methods available today.
Let’s break that down a bit.
How the MVR Process Works
- Evaporation Initiation
The process begins when feed liquid is heated in an evaporator, causing part of it to vaporize. - Vapor Compression
Instead of wasting that vapor, an MVR system compresses it using a mechanical compressor or fan—raising its temperature and pressure. - Heat Reuse
The high-temp vapor is then used to heat the incoming feed via a heat exchanger. This recycles the energy and minimizes the need for external steam or fuel. - Continuous Loop
This loop runs continuously, making the system ideal for large-scale, automated production environments.
🔧 Key MVR Components at a Glance
Component | Function |
---|---|
Evaporator Chamber | Heats and vaporizes feed liquid |
Mechanical Compressor | Compresses vapor to raise temperature |
Heat Exchanger | Transfers vapor heat to incoming liquid |
Condensate Collector | Gathers condensed vapor for reuse or disposal |
Control System | Maintains optimal operation and safety |
Why MVR Is So Efficient Compared to Traditional Methods
If you’re still relying on steam-powered systems like TVR or multi-effect evaporators, you might be losing money and energy every day.
MVR systems can cut energy use by up to 90% compared to traditional evaporators, while improving operational stability and lowering environmental impact.
Let me explain why that matters.
Side-by-Side Comparison: MVR vs. TVR
Factor | MVR | TVR / Multi-Effect |
---|---|---|
Energy Use | Uses only 5–10% of TVR’s energy | High steam consumption |
Cost | Low operating cost, high ROI | High ongoing steam cost |
Temperature | Low-temp, product-safe | Higher risk of thermal damage |
Sustainability | Low carbon footprint | More emissions, more waste |
Maintenance | Requires compressor upkeep | Simpler but less efficient |
In one of our dairy client’s operations, MVR reduced energy consumption so significantly that their ROI period dropped from 3 years to just 14 months. That kind of improvement isn’t hypothetical—it’s happening every day.
Common Industrial Applications for MVR
Whether you’re treating wastewater or concentrating organic liquids, MVR is proving to be one of the most versatile solutions on the market.
Here’s how industries are using MVR to improve their processes and reduce costs:
- Food and Beverage
- Concentrating milk, juice, or sweeteners without degrading flavor or nutrition.
- Example: A plant in New Zealand used three MVR units for 30-day nonstop milk powder production, cutting emissions dramatically.
- Chemical & Pharmaceutical
- Recovering solvents or concentrating active pharmaceutical ingredients (APIs) at controlled temps.
- Wastewater Treatment / ZLD
- Crystalizing high-TDS wastewater, recovering up to 95% of clean water.
- Our client’s 30T/h MVR line treated mixed-salt wastewater, fully compliant with discharge laws.
- Lithium and Battery Recycling
- Recovering valuable salts or purifying extraction liquids at reduced energy cost.
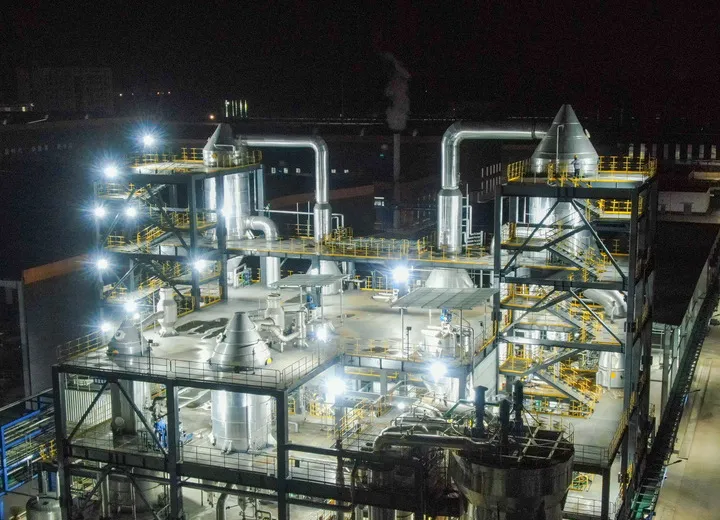
What Is the Difference Between TVR and MVR Evaporators?
Let’s get technical for a moment—because this is where the value becomes crystal clear.
TVR relies on steam-powered jet ejectors, while MVR uses electric compressors to achieve far greater energy efficiency.
Comparison Table: TVR vs. MVR
Aspect | TVR (Thermal Vapor Recompression) | MVR (Mechanical Vapor Recompression) |
---|---|---|
Vapor Compression | Jet ejector using high-pressure steam | Electric-powered compressor or fan |
Energy Source | Steam (high fuel cost) | Electricity (more controllable) |
Efficiency | Moderate (better than single-effect) | High (up to 90% energy savings) |
Cost of Operation | High ongoing cost | Low operational cost |
Product Suitability | High-temp, not for heat-sensitive materials | Ideal for fragile or volatile ingredients |
Initial Investment | Lower capex | Higher capex, but faster ROI |
Space Required | Larger footprint | Compact single-effect layout |
Sustainability | More CO₂ emissions | Lower emissions and water footprint |
Real-World MVR Success: From Concept to Commissioning
At Myande, we’ve helped companies implement MVR in:
- Lithium extraction from salt lakes and ores
- Battery material recycling (nickel/cobalt recovery)
- Textile and electroplating wastewater ZLD
- Tomato paste and sugar syrup concentration
- Biological fermentation broth processing
In each case, MVR gave our clients more than just energy savings—it gave them peace of mind.
Final Thoughts: Is MVR Right for You?
By now, you’re probably wondering: Should I invest in MVR technology for my plant?
If you’re looking to cut costs, reduce emissions, and future-proof your operation, the answer is almost always yes.
MVR is more than a piece of equipment—it’s a smarter approach to industrial evaporation that aligns perfectly with the demands of modern manufacturing. And with the right partner, implementation doesn’t have to be complicated.