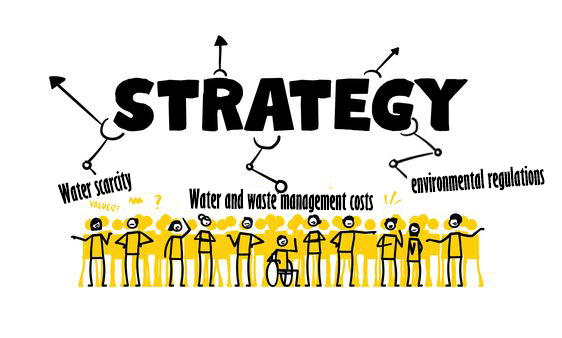
Imagine a world where industrial plants are forced to shut down due to water shortages, where rivers and lakes are polluted beyond repair, and where companies face crippling fines for environmental violations. These scenarios are not far-fetched; they are rapidly becoming the reality for many industries around the globe. Water scarcity, stringent environmental regulations, and the increasing cost of water and waste management are pushing industries to rethink their water use strategies. This is where zero liquid discharge (ZLD) technology comes into play—a transformative approach that not only addresses these pressing issues but also provides a pathway to sustainable industrial practices.
Zero liquid discharge (ZLD) plants are becoming increasingly necessary for industries due to several key reasons:
1. Environmental Protection: ZLD systems treat wastewater by recycling, recovering, and reusing it for industrial purposes, minimizing or eliminating the discharge of liquid waste into the environment. This helps protect water resources and ecosystems from pollution. By ensuring that no liquid waste is released, ZLD systems help industries significantly reduce their environmental footprint.
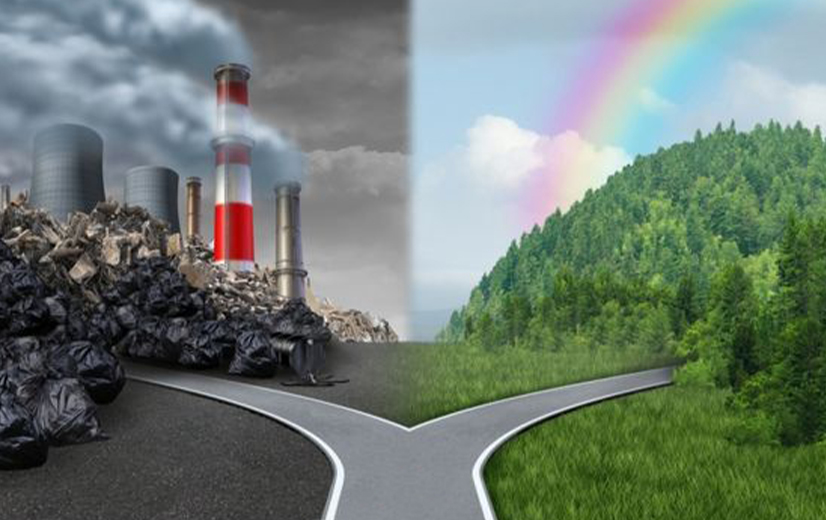
2. Water Scarcity Mitigation: As freshwater resources become scarce, ZLD allows industries to recover and reuse nearly 98% of the water that goes through their industrial systems. This reduces their demand and impact on local water supplies, helping to mitigate water resource insecurity. In regions where water scarcity is a critical issue, ZLD systems provide a sustainable solution for managing water resources efficiently.
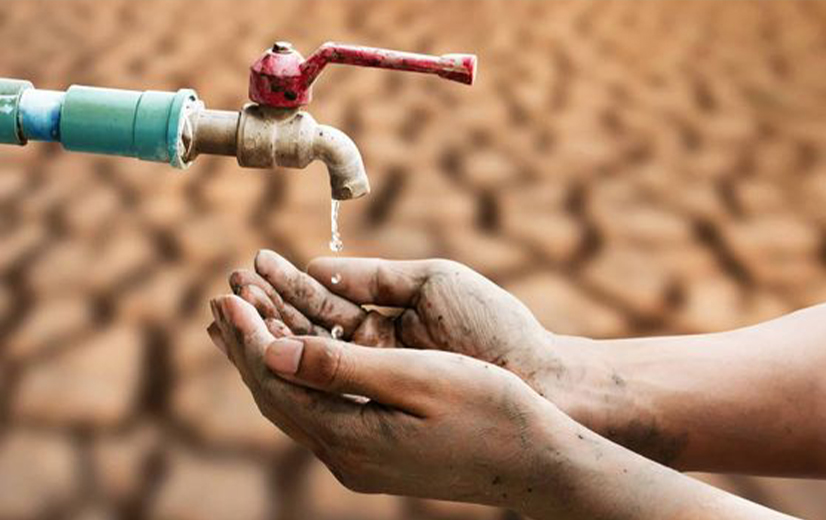
3. Regulatory Compliance: Many countries are implementing stricter environmental regulations that mandate the use of ZLD systems for certain industries. For example, India has required a wide range of industries, including fertilizer, textile, sugar, paper, and power plants, to switch to ZLD treatment processes. Compliance with these regulations is crucial to avoid hefty fines and ensure the continued operation of industrial facilities.
4. Resource Recovery: ZLD systems can help industries recover valuable materials from wastewater, such as lithium, potassium sulfate, gypsum, caustic soda, and sodium sulfate. This can potentially create additional revenue streams. By converting waste into valuable byproducts, ZLD systems not only enhance sustainability but also improve economic viability.
5. Cost Reduction: While ZLD systems require significant upfront investment, they can lead to long-term cost savings by reducing water intake, minimizing waste disposal costs, and potentially recovering valuable byproducts. The initial investment in ZLD technology is offset by the savings and additional revenue generated over time.
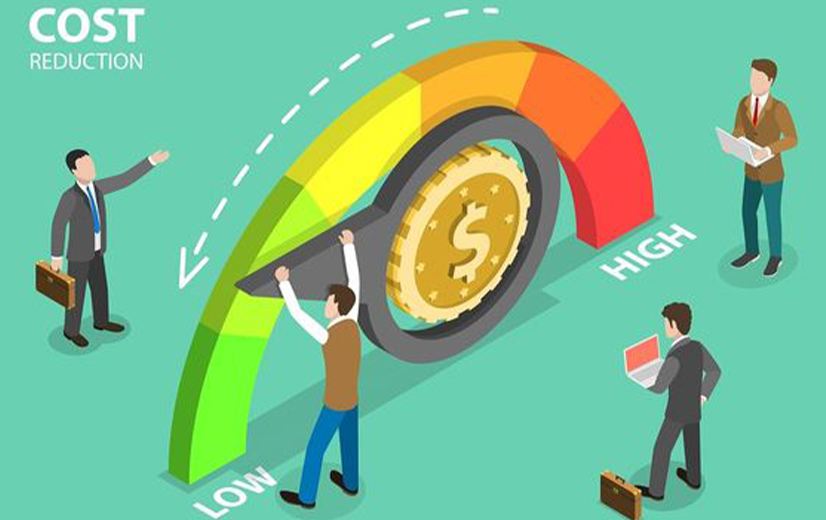
6. Sustainability and Corporate Responsibility: Adopting ZLD technology demonstrates a commitment to sustainable practices and environmental stewardship, which can enhance a company’s reputation and meet growing expectations for corporate responsibility. Companies that invest in ZLD systems are seen as leaders in environmental sustainability, which can be a significant competitive advantage.
7. Operational Risk Mitigation: For industries in water-stressed areas or those with water-intensive processes, ZLD can help insulate operations from escalating source water costs and potential water shortages. By ensuring a reliable supply of recycled water, ZLD systems provide operational stability and resilience.
8. Addressing Complex Waste Streams: ZLD is particularly effective for managing challenging wastewaters produced by industries such as power generation, chemical manufacturing, and electroplating, which may contain high levels of contaminants or toxic materials. ZLD systems are designed to handle these complex waste streams, ensuring that all contaminants are effectively removed and converted into solid waste.
While ZLD systems can be complex and require significant initial investment, they are increasingly seen as a necessary solution for industries facing water scarcity, stringent regulations, and growing environmental concerns. The global market for ZLD systems is expected to grow significantly in the coming years, reflecting the rising importance of this technology in industrial water management.
Understanding the necessity of zero liquid discharge (ZLD) systems is just the beginning. To fully appreciate the impact and implementation of ZLD technology, it is essential to explore its applications in specific industries. From the fertilizer sector to pharmaceutical manufacturing, ZLD systems play a critical role in managing wastewater, recovering valuable resources, and ensuring regulatory compliance. Let’s delve deeper into how ZLD technology is applied in these industries and the technological advancements driving its adoption.
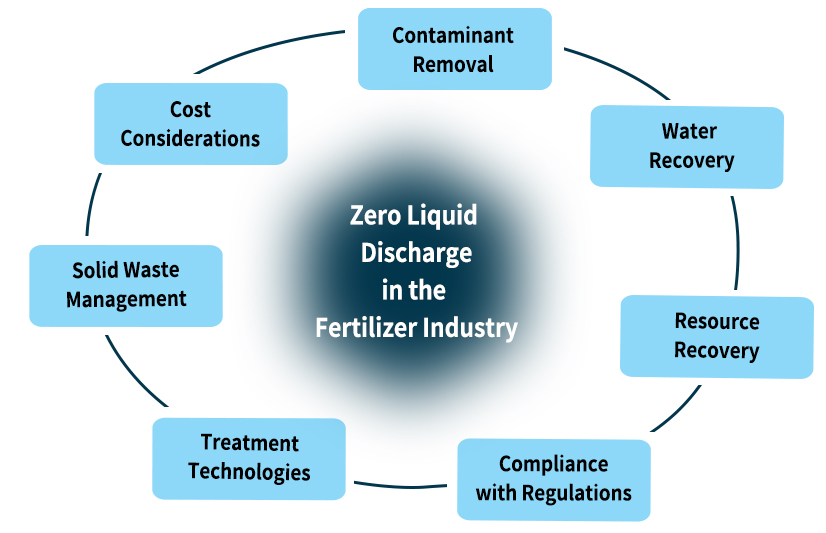
What is Zero Liquid Discharge in the Fertilizer Industry?
Zero liquid discharge (ZLD) in the fertilizer industry refers to a wastewater treatment process that eliminates all liquid waste from fertilizer production, recovering and reusing water while converting contaminants into solid waste. This approach is particularly important for the fertilizer industry due to the nature of its effluents and increasing environmental regulations.
1. Contaminant Removal: Fertilizer industry effluents typically contain pollutants such as ammonia, ammonium salts, nitrates, urea, chromates, phosphates, heavy metals, and suspended solids. ZLD systems are designed to treat and remove these contaminants effectively. Advanced treatment technologies ensure that all harmful substances are removed, protecting water bodies from pollution.
2. Water Recovery: ZLD processes aim to recover and reuse nearly all the water from the industrial wastewater, reducing the demand on freshwater resources and minimizing environmental impact. By recycling water within the production process, fertilizer plants can significantly reduce their freshwater consumption.
3. Resource Recovery: ZLD systems in the fertilizer industry can help recover valuable materials from wastewater, such as silica, which can be used in applications like chromatography and as reinforcing material. This not only reduces waste but also generates additional revenue from recovered materials.
4. Compliance with Regulations: Many countries are implementing stricter environmental regulations that require fertilizer industries to adopt ZLD or near-ZLD processes to minimize their environmental impact. Compliance with these regulations is essential for the continued operation and growth of fertilizer plants.
5. Treatment Technologies: ZLD systems in the fertilizer industry typically involve a combination of technologies such as clarification, chemical precipitation, filtration, reverse osmosis, and evaporation/crystallization. These technologies work together to ensure that all contaminants are removed and water is effectively recycled.
6. Solid Waste Management: The end result of a ZLD process is a dry, solid cake containing concentrated contaminants, which requires proper disposal or potential further treatment for resource recovery. Effective management of solid waste is crucial to the success of ZLD systems.
7. Cost Considerations: While ZLD systems require significant initial investment, they can lead to long-term benefits such as reduced water intake costs, minimized waste disposal expenses, and potential recovery of valuable byproducts. The economic benefits of ZLD systems often outweigh the initial investment.
Implementing ZLD in the fertilizer industry is driven by the necessity to address environmental concerns, comply with regulations, and manage water resources more sustainably. As water scarcity and environmental regulations become more pressing, ZLD systems are likely to become increasingly important for the fertilizer industry’s long-term sustainability and operational viability.
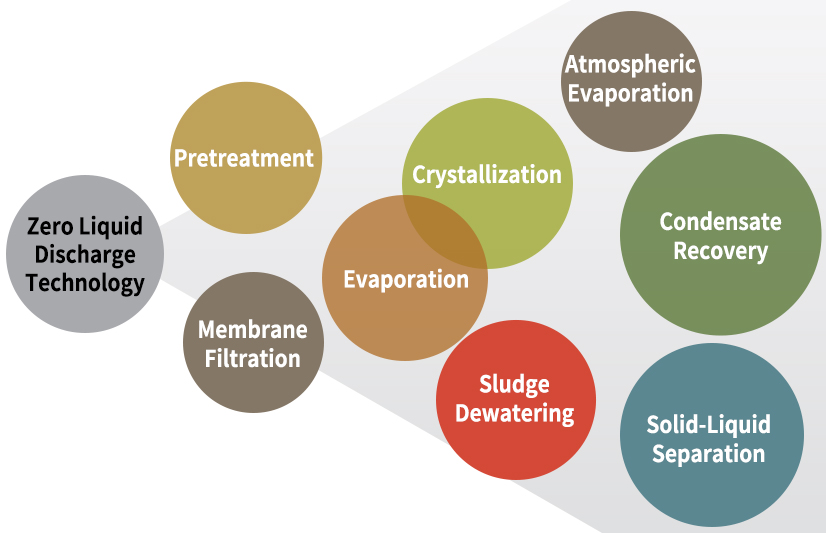
What is the Technology of ZLD?
Zero Liquid Discharge (ZLD) is an advanced wastewater treatment process that aims to eliminate all liquid waste from industrial operations. The key technologies and components of a typical ZLD system include:
1. Pretreatment
This initial stage may involve processes like clarification, chemical precipitation, and filtration to remove suspended solids and other contaminants that could interfere with downstream processes. Effective pretreatment is essential for the smooth functioning of subsequent stages.
2. Membrane Filtration
Technologies such as ultrafiltration (UF) and reverse osmosis (RO) are used to remove dissolved solids and concentrate the wastewater. Reverse osmosis is particularly effective at separating water from dissolved salts and other contaminants. Membrane filtration ensures that the water recovered is of high purity and suitable for reuse.
3. Evaporation
Thermal evaporators, often falling film evaporators or brine concentrators, are used to further concentrate the wastewater by evaporating water and leaving behind a more concentrated brine solution. This step is crucial for reducing the volume of liquid waste.
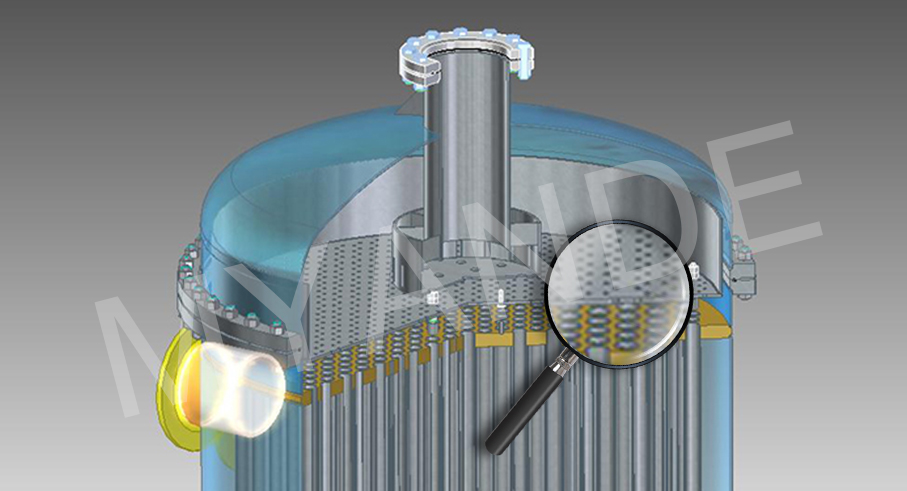
4. Crystallization
Crystallizers are employed to process the concentrated brine from the evaporators, forming solid crystals from the remaining dissolved solids. This solid waste can then be managed appropriately, ensuring that no liquid waste is discharged.
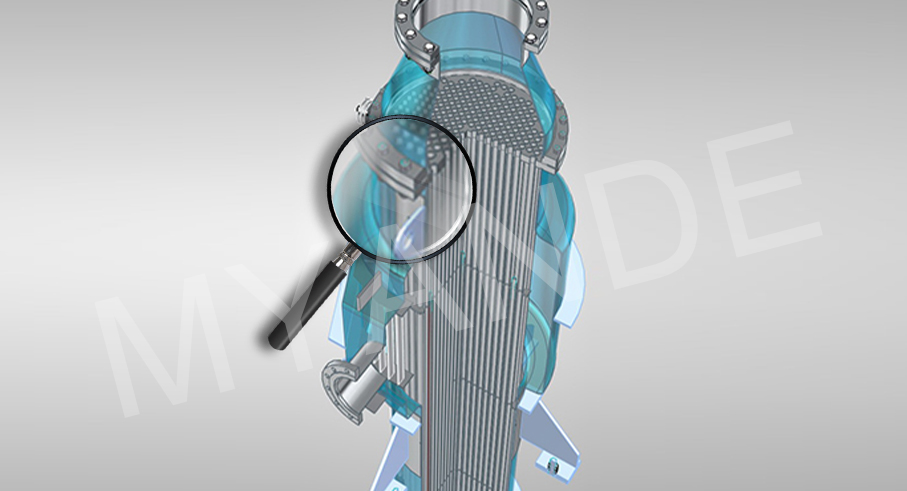
5. Solid-Liquid Separation
Technologies like filter presses or centrifuges are used to separate the crystallized solids from any remaining liquid. Efficient solid-liquid separation ensures that the final solid waste is dry and easy to handle.
6. Condensate Recovery
The water vapor produced during evaporation and crystallization is condensed and recovered as high-purity distillate, which can be reused in industrial processes. Condensate recovery maximizes water reuse and minimizes the need for freshwater intake.
7. Sludge Dewatering
Filter presses or other dewatering equipment are used to remove moisture from the solid waste produced, creating a dry cake suitable for disposal or potential reuse. Effective sludge dewatering reduces the volume of waste that needs to be managed.
8. Atmospheric Evaporation
In some cases, atmospheric evaporators may be used as a final polishing step or for handling smaller volumes of wastewater. This step ensures that even the smallest quantities of wastewater are treated effectively.
The specific combination and configuration of these technologies can vary depending on the characteristics of the wastewater being treated and the industry’s requirements. ZLD systems are designed to recover and reuse nearly all the water from industrial wastewater while converting contaminants into solid waste, thus eliminating liquid discharge and conserving water resources.
Conclusion
In conclusion, the necessity of Zero Liquid Discharge (ZLD) plants for industries cannot be overstated. ZLD systems address some of the most pressing environmental and operational challenges faced by modern industries, from environmental protection and water scarcity mitigation to regulatory compliance and resource recovery. By leveraging advanced technologies, ZLD systems transform wastewater management into a sustainable and economically viable practice, supporting industries in their journey towards sustainability and responsible resource use.